Saltwater
Member level 3
Hello,
I want to have a board to board connection that tops out at about 38MHz.
I want to make it as low jitter as possible. But not being formally educated in electronics I wanted to run this by the forum to see if I didnt do something horribly wrong. (Which is very possible)..
Also..Is there a way to guestimate or calculate the right RC values for the range of max 25MHz to 38MHz and possibly smaller?
And is this or the revised version worth building over an optical connection. (albeit for the master clock)?
So.. Here's what I hacked together..
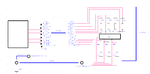
I want to have a board to board connection that tops out at about 38MHz.
I want to make it as low jitter as possible. But not being formally educated in electronics I wanted to run this by the forum to see if I didnt do something horribly wrong. (Which is very possible)..
Also..Is there a way to guestimate or calculate the right RC values for the range of max 25MHz to 38MHz and possibly smaller?
And is this or the revised version worth building over an optical connection. (albeit for the master clock)?
So.. Here's what I hacked together..
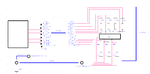