Vermes
Advanced Member level 4
Epoxy, commonly used in electronics and electrical systems, is the basic component of polyepoxides. It is a very important component in many kinds of work in this field, such as building motors, generators, transformers, insulators and many others. Electrical insulation ensured by epoxy prevents from short circuits and also protects the electrical equipment from undesired impact of dust and water.
Let us present the alternatives we have for flip-chip mounting. We have non-conductive epoxy, conductive epoxy, thermocompression attach and thermosonic compression.
What is a flip-chip mounting method?
The flip-chip mounting is also known as controlled collapse chip connection. It is a method for interconnecting semiconductor devices such as IC chips or MEMS. Please look at some pictures in google which show what problem do we face:
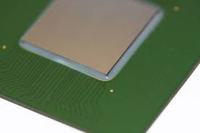
All of us know this chip. It is a basic processor like Intel, AMD etc. On its edge we can see some kind of glue, paste. The next picture will show you a better view of what do we need to do:
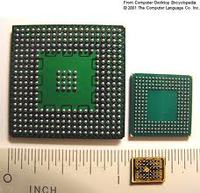
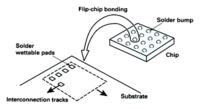
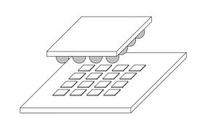
When you want to mount a similar chip to external circuit board or another chip, you have to flip it over to face down its upper side. What more, its pads have to be aligned with matching pads of the external circuit. Remembering that integrated circuits are usually put on a wafer, then pads have to be metalized on the surface in order to become more receptive to soldering. Every pad has its solder dots. Then the chips should be cut and flip to be placed in correct positions to make it sure that the solder balls face the connectors, which should be remelted then to produce the electrical connection. After remelting, there is a small gap created between the circuitry of the chip and the mounting placed under it. The last thing you have to do in order to create the mounting is to underfill the gaps using adhesive which is to be an electrical insulator. The insulator is to ensure strong mechanical connection.
In few words, when you want to fill the emptiness between the chip and the package and to fill the space around the gold bumps, non-conductive epoxy is the best solution, because it helps you to fill the space without the risk that these elements do contact.
Thanks to its natural features, epoxy shrinks and thus provides the best holding together both the chip and the package. Its chemical model and its capacity to form tight cross-linked polymer structure explains its specific features such as strength, resistance, flexibility and of course strong adhesive properties.
Non-conductive epoxy is commonly used for electrical insulation when you want to glue SMD components to a PCB. It is a kind of a dielectric dam as well as a solder mask. Another application is mentioned above filling gaps.
Non-conductive epoxy may be also extremely useful when you want to for example fix a broken PCB and it is important to use an adhesive that does not conduct in order not to interfere the paths we already have on a PCB. When epoxy is cured, it acts as an electrical insulator which is not only very effective, but also provides good high temperature, mechanical and impact resistance. It means the using non-conductive epoxy you make it sure that your work will be improved with its good quality and performance. It can be used for all the following kinds of PCB damages: gaps, holes or even burns. This epoxy is the best material which is flexible and also ensures a protection against breaking and melting. These characteristics make non-conductive epoxy a common component of popular PCB repair kits.
To sum up, there are many application of non-conductive epoxy, what makes this universal adhesive the best one, impossible to be replaced with another in every lab workshop.
Let us present the alternatives we have for flip-chip mounting. We have non-conductive epoxy, conductive epoxy, thermocompression attach and thermosonic compression.
What is a flip-chip mounting method?
The flip-chip mounting is also known as controlled collapse chip connection. It is a method for interconnecting semiconductor devices such as IC chips or MEMS. Please look at some pictures in google which show what problem do we face:
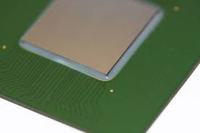
All of us know this chip. It is a basic processor like Intel, AMD etc. On its edge we can see some kind of glue, paste. The next picture will show you a better view of what do we need to do:
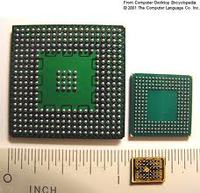
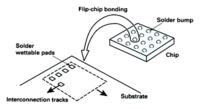
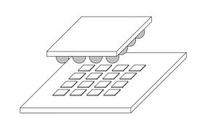
When you want to mount a similar chip to external circuit board or another chip, you have to flip it over to face down its upper side. What more, its pads have to be aligned with matching pads of the external circuit. Remembering that integrated circuits are usually put on a wafer, then pads have to be metalized on the surface in order to become more receptive to soldering. Every pad has its solder dots. Then the chips should be cut and flip to be placed in correct positions to make it sure that the solder balls face the connectors, which should be remelted then to produce the electrical connection. After remelting, there is a small gap created between the circuitry of the chip and the mounting placed under it. The last thing you have to do in order to create the mounting is to underfill the gaps using adhesive which is to be an electrical insulator. The insulator is to ensure strong mechanical connection.
In few words, when you want to fill the emptiness between the chip and the package and to fill the space around the gold bumps, non-conductive epoxy is the best solution, because it helps you to fill the space without the risk that these elements do contact.
Thanks to its natural features, epoxy shrinks and thus provides the best holding together both the chip and the package. Its chemical model and its capacity to form tight cross-linked polymer structure explains its specific features such as strength, resistance, flexibility and of course strong adhesive properties.
Non-conductive epoxy is commonly used for electrical insulation when you want to glue SMD components to a PCB. It is a kind of a dielectric dam as well as a solder mask. Another application is mentioned above filling gaps.
Non-conductive epoxy may be also extremely useful when you want to for example fix a broken PCB and it is important to use an adhesive that does not conduct in order not to interfere the paths we already have on a PCB. When epoxy is cured, it acts as an electrical insulator which is not only very effective, but also provides good high temperature, mechanical and impact resistance. It means the using non-conductive epoxy you make it sure that your work will be improved with its good quality and performance. It can be used for all the following kinds of PCB damages: gaps, holes or even burns. This epoxy is the best material which is flexible and also ensures a protection against breaking and melting. These characteristics make non-conductive epoxy a common component of popular PCB repair kits.
To sum up, there are many application of non-conductive epoxy, what makes this universal adhesive the best one, impossible to be replaced with another in every lab workshop.