bmmm
Newbie level 3
Hello,
I am laying the PCB in CADstar 12.1 Express. As a beginner, I need help on the following questinos:
1)how can i set the copper trace width of a signal (eg: VCC, GND, etc)? Is there a quicker way than setting the width manually in every connection?
2)How can I specify the V-grooving and CNC routing of the PCB? Which layer should I draw the v-groving traces on? Which layer should I draw the CNC route on?
3)If I dont want the ground plate automatically connects to the un-connected pins, where can I configure this?
4)In PCB routing, when I am routing a trace between two pin, why the trace can only exiting the pad from two directions only? ie (can only go East or West in fig1). To have more flexibility in routing, the trace exiting from the square pad should be able go in any direction. What have I done wrong?
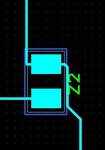
Thank you!
Q
I am laying the PCB in CADstar 12.1 Express. As a beginner, I need help on the following questinos:
1)how can i set the copper trace width of a signal (eg: VCC, GND, etc)? Is there a quicker way than setting the width manually in every connection?
2)How can I specify the V-grooving and CNC routing of the PCB? Which layer should I draw the v-groving traces on? Which layer should I draw the CNC route on?
3)If I dont want the ground plate automatically connects to the un-connected pins, where can I configure this?
4)In PCB routing, when I am routing a trace between two pin, why the trace can only exiting the pad from two directions only? ie (can only go East or West in fig1). To have more flexibility in routing, the trace exiting from the square pad should be able go in any direction. What have I done wrong?
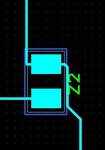
Thank you!
Q