meeyaw
Junior Member level 3
Hi,
I am currently analysing current density of the CMOS shown below. It is using a multi-finger layout technique.
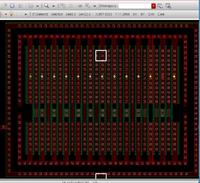
Can you help me explain why the current is only concentrated on one finger only, thus exceeding the allowable current in that given size of metal?
I thought that current throughout the fingers of the MOS is the same
By the way, the image is a sample of a buffer.
Note: Red mark denotes the area wherein the area that sinks largest current in the entire cell
I am currently analysing current density of the CMOS shown below. It is using a multi-finger layout technique.
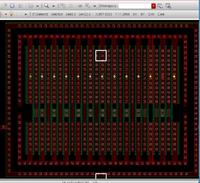
Can you help me explain why the current is only concentrated on one finger only, thus exceeding the allowable current in that given size of metal?
I thought that current throughout the fingers of the MOS is the same
By the way, the image is a sample of a buffer.
Note: Red mark denotes the area wherein the area that sinks largest current in the entire cell