matrixofdynamism
Advanced Member level 2
I need input from a NES controller. Since the connector at end of a NES controller is custom for the console it is used with, I severed the connector and soldered the wires to a DB9 connector. I also got a shell for the connector as show below:
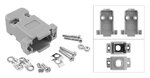
I expected that the shell shall hold the wire tight once it is closed and screwed. However, I found that the wire of the controller was very thin. Although it has been soldered to the DB9 connector, it will break if limited force is applied. Since the shell does not "hold onto" the wire so any pulling force is resisted, I am afraid that the connection is not reliable.
Game controllers are likely to get pulled with from time and again. What should I do now?
In case you are wondering, this is what a NES controller looks like:
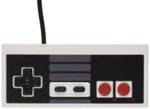
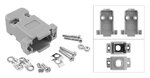
I expected that the shell shall hold the wire tight once it is closed and screwed. However, I found that the wire of the controller was very thin. Although it has been soldered to the DB9 connector, it will break if limited force is applied. Since the shell does not "hold onto" the wire so any pulling force is resisted, I am afraid that the connection is not reliable.
Game controllers are likely to get pulled with from time and again. What should I do now?
In case you are wondering, this is what a NES controller looks like:
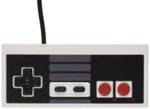