stringerbell
Junior Member level 1
I was wondering if any of you could help me understand a bit more how the IRKT 91 12 "back to back SCR" can be driven in a cost effective way. I have found this circuit on a closed tread on here:
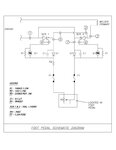
I'm not understanding all of what im reading, i just watched some 1 hour explanation to zero crossing in ac systems, and its importance in scr switching, if i understand correctly the capacitors give the delay the gates need in the above circuit, to prevent a a short, i see gate drivers online like this one
https://www.nuwaveproducts.com/Data...ower-Control-Gate-Driver-Board-Zero-Cross.pdf
If im understanding correctly i could simply input 0-5v and it will take care of the rest. This looks like the way i would like to add an arduino down the road will this work? i have also seen complex arduino projects with complex for me zero crossing circuits and pulse train drivers with coding way beyond my ability.
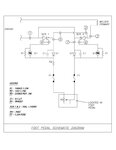
I'm not understanding all of what im reading, i just watched some 1 hour explanation to zero crossing in ac systems, and its importance in scr switching, if i understand correctly the capacitors give the delay the gates need in the above circuit, to prevent a a short, i see gate drivers online like this one
https://www.nuwaveproducts.com/Data...ower-Control-Gate-Driver-Board-Zero-Cross.pdf
If im understanding correctly i could simply input 0-5v and it will take care of the rest. This looks like the way i would like to add an arduino down the road will this work? i have also seen complex arduino projects with complex for me zero crossing circuits and pulse train drivers with coding way beyond my ability.
Last edited by a moderator: