apollo_111
Newbie level 4

- Joined
- Mar 11, 2014
- Messages
- 6
- Helped
- 0
- Reputation
- 0
- Reaction score
- 0
- Trophy points
- 1
- Activity points
- 43
Hi friends.
I have trouble with my boost converter+inverter design. My boost converter is work proper itself but when I try to connect a full bridge inverter to output of the converter, converter output voltage dramatically drops down. Actually, I'm trying to have 220Vrms AC voltage from inverter output.
I'm waiting your help please.
My design without inverter (Boost converter output voltage is nearly 60V):
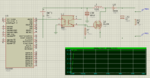
After connecting the full bridge inverter:
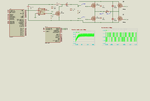
I have trouble with my boost converter+inverter design. My boost converter is work proper itself but when I try to connect a full bridge inverter to output of the converter, converter output voltage dramatically drops down. Actually, I'm trying to have 220Vrms AC voltage from inverter output.
I'm waiting your help please.
My design without inverter (Boost converter output voltage is nearly 60V):
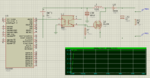
After connecting the full bridge inverter:
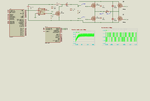