SBTECH
Newbie level 6
- Joined
- Feb 17, 2010
- Messages
- 12
- Helped
- 0
- Reputation
- 0
- Reaction score
- 0
- Trophy points
- 1,281
- Location
- Istanbul, Turkey
- Activity points
- 1,390
Dear All,
I am designing a relay switching board whick will switch 230 V AC 5A Motors. In my PCB Design, I am trying to use one layer 2 oz/ft^2 copper.
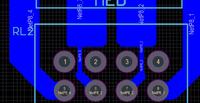
I am just guessing if such a routing as in the attachement is dangerous or not ? For 5A current , I need to have 100 mil tracks. But between relay's contact i had to do such a routing. For example for NetP8_3, I started with 50 mil width from Pad 6 and routed for 3.5 mm length , then routed for 3.5 mm length with 25 mil track width , than i continue with a polygon pour.
Do you think that cause any problems ?
Thanks very much for all your helps..
I am designing a relay switching board whick will switch 230 V AC 5A Motors. In my PCB Design, I am trying to use one layer 2 oz/ft^2 copper.
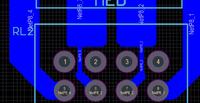
I am just guessing if such a routing as in the attachement is dangerous or not ? For 5A current , I need to have 100 mil tracks. But between relay's contact i had to do such a routing. For example for NetP8_3, I started with 50 mil width from Pad 6 and routed for 3.5 mm length , then routed for 3.5 mm length with 25 mil track width , than i continue with a polygon pour.
Do you think that cause any problems ?
Thanks very much for all your helps..