powersys
Advanced Member level 1
I wish to measure the vibration of an electric motor as shown in figure below. One of the accelerometers (red) is placed at the location as shown in the figure. The accelerometers are manufactured by PCB. They are connected to a power unit and from the power unit their signals are fed to Agilent Dynamic Signal Analyser 35670A for frequency domain analysis using FFT.
A vibration peak is expected to be observed at frequency 500Hz. The number of average measurement taken is 20. I manage to measure this peak.
I repeat the test, with similar setup, settings, and assembly program, many times (morning, afternoon, night; monday, tuesday,...etc). The accelerometer was never removed from the setup and it was at the same location in all those tests. I found the amplitude of the peak at 500Hz is not consistent. The lowest measured value is 110 (uVrms), whilst the highest value can be up to 160 (uVrms). The supply to the load machine was monitored closely so that it exerted a constant load to the motor under test. In my opinion, the difference (50uVrms) is too high and I suspect something wrong with my experiment. But I could not find out the causes of the inconsistency. Therefore, I will really appreciate if you guys can share your practical experience when performing vibration test with accelerometer.
By the way I wish to understand more the following issues. Kindly advise which reference book that covers the following subjects.
PRACTICAL ISSUES
3.1 Selecting the right parameter
3.2 Problems in simple usage (portable monitoring with vibration meter or data collector)
3.3 Repeatability (portable monitoring)
3.3.1 Non-repeatability due to machine condition
a. Background vibration
b. Effect of machine speed and load, etc.
c. Variation of signal at nominally constant operating conditions Time domain averaging Process domain averaging
d. Trending of data
3.3.2 Non-repeatability due to measurement technique
a. Mounting of transducer
b. Temperature effects
c. Spurious low frequency 'Ski-slope' effect
d. Saturation of the conditioning electronics
3.4 Experience with permanent monitors
3.5 Implementation of permanent monitors
Thank you very much
A vibration peak is expected to be observed at frequency 500Hz. The number of average measurement taken is 20. I manage to measure this peak.
I repeat the test, with similar setup, settings, and assembly program, many times (morning, afternoon, night; monday, tuesday,...etc). The accelerometer was never removed from the setup and it was at the same location in all those tests. I found the amplitude of the peak at 500Hz is not consistent. The lowest measured value is 110 (uVrms), whilst the highest value can be up to 160 (uVrms). The supply to the load machine was monitored closely so that it exerted a constant load to the motor under test. In my opinion, the difference (50uVrms) is too high and I suspect something wrong with my experiment. But I could not find out the causes of the inconsistency. Therefore, I will really appreciate if you guys can share your practical experience when performing vibration test with accelerometer.
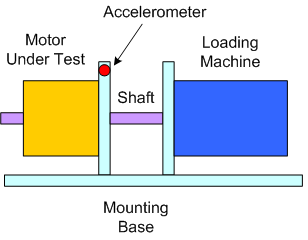
By the way I wish to understand more the following issues. Kindly advise which reference book that covers the following subjects.
PRACTICAL ISSUES
3.1 Selecting the right parameter
3.2 Problems in simple usage (portable monitoring with vibration meter or data collector)
3.3 Repeatability (portable monitoring)
3.3.1 Non-repeatability due to machine condition
a. Background vibration
b. Effect of machine speed and load, etc.
c. Variation of signal at nominally constant operating conditions Time domain averaging Process domain averaging
d. Trending of data
3.3.2 Non-repeatability due to measurement technique
a. Mounting of transducer
b. Temperature effects
c. Spurious low frequency 'Ski-slope' effect
d. Saturation of the conditioning electronics
3.4 Experience with permanent monitors
3.5 Implementation of permanent monitors
Thank you very much