d123
Advanced Member level 5
Hi,
I'm making a simple wind speed sensor using a 5V DC solar motor (max. 55mA). The op amp for testing is an LM324, but in real circuit will be a rail-to-rail input and output LMC6464 as need to be sure output is over minimum for CD4000 5V logic high signal (3.5V), so LM324 not quite reliable for this (3.5V out max. at +5Vs).
Want to keep whole circuit on single +5V supply for sake of simplicity, and to be able to tie several sensor grounds to same ground as several comparators and a few CD4000 logic gates.
It shouldn't ever happen (like the Titanic), but to be safe in case the wind ever blows the anemometer cups counter-clockwise and creates an inverted polarity signal, there is a full-wave rectifier between the motor and the comparator.
In principle the circuit is working okay, but I have a doubt as to whether when the motor spins counter-clockwise this has any effect on the supply rail or adjacent ICs, despite the DMM readings to the contrary - the whole sensing circuit is that in the schematic along with several other comparators fed from different analog sensors.
In the image there is the schematic, and a small table with measured results from spinning the motor with my fingers, enough to get a reasonable voltage in both directions.
From what I see, the motor counter-clockwise direction and inverted polarity output is having no effect on the supply rails, it seems too good to be true, which is why I'm asking if this circuit is a sound design.
Also, given the difference in voltage between positive input and negative input - Do I need to place a 10K resistor from the non-inverting input to ground, or from motor "ground"/black terminal to ground to balance the signals? Ask because... Not sure if what happens is relevant to electrical issue, or is mechanical and idiosyncratic to this motor: the motor spins far easier CCW than CW, which is reason for asking about need for balancing resistors somewhere in circuit.
Thanks.
- - - Updated - - -
Apologies, it was right under my nose: the diode was causing the voltage difference... Have attached updated schematic with updated DMM readings.
First question still applies: Is this circuit a valid/functionally acceptable design, and when/if motor runs CCW will not have a negative (no pun intended) effect on the supply rail or other parts of the whole circuit, please? Thanks.
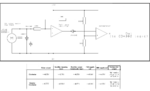
I'm making a simple wind speed sensor using a 5V DC solar motor (max. 55mA). The op amp for testing is an LM324, but in real circuit will be a rail-to-rail input and output LMC6464 as need to be sure output is over minimum for CD4000 5V logic high signal (3.5V), so LM324 not quite reliable for this (3.5V out max. at +5Vs).
Want to keep whole circuit on single +5V supply for sake of simplicity, and to be able to tie several sensor grounds to same ground as several comparators and a few CD4000 logic gates.
It shouldn't ever happen (like the Titanic), but to be safe in case the wind ever blows the anemometer cups counter-clockwise and creates an inverted polarity signal, there is a full-wave rectifier between the motor and the comparator.
In principle the circuit is working okay, but I have a doubt as to whether when the motor spins counter-clockwise this has any effect on the supply rail or adjacent ICs, despite the DMM readings to the contrary - the whole sensing circuit is that in the schematic along with several other comparators fed from different analog sensors.
In the image there is the schematic, and a small table with measured results from spinning the motor with my fingers, enough to get a reasonable voltage in both directions.
From what I see, the motor counter-clockwise direction and inverted polarity output is having no effect on the supply rails, it seems too good to be true, which is why I'm asking if this circuit is a sound design.
Also, given the difference in voltage between positive input and negative input - Do I need to place a 10K resistor from the non-inverting input to ground, or from motor "ground"/black terminal to ground to balance the signals? Ask because... Not sure if what happens is relevant to electrical issue, or is mechanical and idiosyncratic to this motor: the motor spins far easier CCW than CW, which is reason for asking about need for balancing resistors somewhere in circuit.
Thanks.
- - - Updated - - -
Apologies, it was right under my nose: the diode was causing the voltage difference... Have attached updated schematic with updated DMM readings.
First question still applies: Is this circuit a valid/functionally acceptable design, and when/if motor runs CCW will not have a negative (no pun intended) effect on the supply rail or other parts of the whole circuit, please? Thanks.
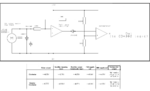