rocky79
Member level 5

- Joined
- Sep 20, 2010
- Messages
- 83
- Helped
- 1
- Reputation
- 2
- Reaction score
- 0
- Trophy points
- 1,286
- Activity points
- 1,903
I have been looking for a level 4 ESD pin protection on microcontroller pin( pic16f1503).
The micro digital input pin is used to measure pulses between 50us to 200us.
Do you think a circuit like this would work?
R=500 ohms and
C=0.01uF
VESD=V0=15kv ( Level 4)
Vc=V0(1-e^(-t/RC))
Ic=(V0/R)*e^(-t/RC)
the RC filter will take 1.67uS to charge to 5v however the deadly spikes only last 10’s of nano-seconds.
The initial spike current at t=0 is V0/R=(15kv/500)=30 amps.
In order to conduct this damaging current away from the protected component I added a TVS diode in parallel with the RC.
What do you think about this TVS from littlefuse part# SD05C it has 5v reverse working voltage and clamp at 14.5v 10amps?
Any other suggestions will be appreciated.
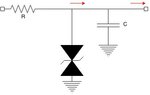
**broken link removed**
The micro digital input pin is used to measure pulses between 50us to 200us.
Do you think a circuit like this would work?
R=500 ohms and
C=0.01uF
VESD=V0=15kv ( Level 4)
Vc=V0(1-e^(-t/RC))
Ic=(V0/R)*e^(-t/RC)
the RC filter will take 1.67uS to charge to 5v however the deadly spikes only last 10’s of nano-seconds.
The initial spike current at t=0 is V0/R=(15kv/500)=30 amps.
In order to conduct this damaging current away from the protected component I added a TVS diode in parallel with the RC.
What do you think about this TVS from littlefuse part# SD05C it has 5v reverse working voltage and clamp at 14.5v 10amps?
Any other suggestions will be appreciated.
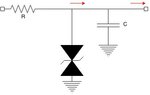
**broken link removed**
Last edited: