Omar El Kelany
Newbie level 6

- Joined
- Nov 29, 2012
- Messages
- 12
- Helped
- 0
- Reputation
- 0
- Reaction score
- 0
- Trophy points
- 1,281
- Activity points
- 1,377
I am working on BLDC motor driver...using three ir2110 with igbt HGTG30N60C3D...motor is around 400W ..48volt...Boot strap cap. 100uf(big i know).
I tried first to run without hall but couldn't adjust it to run properely...kept misfiring and shaking...so i decided to use hall sensors for better control...i wrote the code..tested the sequence and sure no problem with that...the problem is that the motor rotates for less than a second and one ir2110 is damaged...if i try to buzz across the gate and emitter..it gives a buzz(short circuit) ..if i remove the damaged ir2110 and buzz no buzz, if i replace with a new one...also no buzz, can't figure out the reason why ir2110 is damaged every time. tried with frequency about 35 hz and 500 hz..with duty cycle ranging from 20% to 60%
so i want to ask about
1)what happens if the bootstrap is too large
2)what can cause such problem to happen
Attached half bridge "as i use three half bridges"
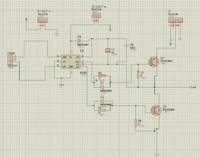
I tried first to run without hall but couldn't adjust it to run properely...kept misfiring and shaking...so i decided to use hall sensors for better control...i wrote the code..tested the sequence and sure no problem with that...the problem is that the motor rotates for less than a second and one ir2110 is damaged...if i try to buzz across the gate and emitter..it gives a buzz(short circuit) ..if i remove the damaged ir2110 and buzz no buzz, if i replace with a new one...also no buzz, can't figure out the reason why ir2110 is damaged every time. tried with frequency about 35 hz and 500 hz..with duty cycle ranging from 20% to 60%
so i want to ask about
1)what happens if the bootstrap is too large
2)what can cause such problem to happen
Attached half bridge "as i use three half bridges"
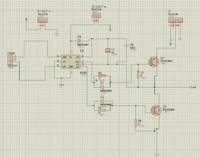