Bjtpower
Full Member level 5
Dear Sir
I have developing the Flyback converter in
open loop.
attached image is the Result observed at 70v (Dc) Input.
The waveform is of the Voltage across drain to source i have used the Diode-Zener Snubber but still there are some ringing as you can observe in the Image attached.
Kindly help how to reduce the same as well the causes of ringing In vds so i can Remove the same & Go for the Output.
I have developing the Flyback converter in
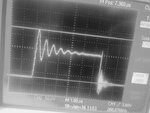
attached image is the Result observed at 70v (Dc) Input.
The waveform is of the Voltage across drain to source i have used the Diode-Zener Snubber but still there are some ringing as you can observe in the Image attached.
Kindly help how to reduce the same as well the causes of ringing In vds so i can Remove the same & Go for the Output.