KESV
Newbie level 5
- Joined
- Aug 26, 2015
- Messages
- 9
- Helped
- 0
- Reputation
- 0
- Reaction score
- 0
- Trophy points
- 1
- Location
- Bergen, Norway
- Activity points
- 84
Hi all,
I'm new to this forum and hope that you can help me.
I'm in the process of building a control cabinet for my home brewery. The brewery consists of three heating elements (3500W) but I only have available two 16A power feeds (220V, living in Norway).
The heating elements are controlled by 3 switches (SW1, SW2, SW3) and 4 contactors (K1, K2, K3 and K4), where K1 is for heater 1, K2 & K3 are for Heater 2 and K4 is for heater 3. The three switches are on my drawing showed as NO, but can I can add more NC or NO to these.
I've created a logic on how this should work, with switching sequence in left column. The main areas of concern is that K1&K2 must never activate at the same time. This also applies to K2&K3 and K3&K4. All the contactor have additional 1xNO and 1xNC that can be used. If needed I can also add more relays. The control voltage for the contactors are 24VDC.
Attached is also a ladder diagram showing my thinking, but I'm stuck. No matter how hard I try I'm not able to solve this, it has been too long since my electronic exams.
Maybe not a very good description, but I hope it's understandable.
I'm very grateful for any help, my brewing of beer depends on this ;-)
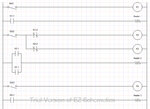
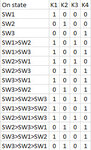
I'm new to this forum and hope that you can help me.
I'm in the process of building a control cabinet for my home brewery. The brewery consists of three heating elements (3500W) but I only have available two 16A power feeds (220V, living in Norway).
The heating elements are controlled by 3 switches (SW1, SW2, SW3) and 4 contactors (K1, K2, K3 and K4), where K1 is for heater 1, K2 & K3 are for Heater 2 and K4 is for heater 3. The three switches are on my drawing showed as NO, but can I can add more NC or NO to these.
I've created a logic on how this should work, with switching sequence in left column. The main areas of concern is that K1&K2 must never activate at the same time. This also applies to K2&K3 and K3&K4. All the contactor have additional 1xNO and 1xNC that can be used. If needed I can also add more relays. The control voltage for the contactors are 24VDC.
Attached is also a ladder diagram showing my thinking, but I'm stuck. No matter how hard I try I'm not able to solve this, it has been too long since my electronic exams.
Maybe not a very good description, but I hope it's understandable.
I'm very grateful for any help, my brewing of beer depends on this ;-)
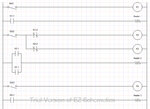
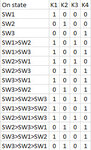