Alper özel
Member level 1
- Joined
- Feb 28, 2015
- Messages
- 40
- Helped
- 0
- Reputation
- 0
- Reaction score
- 0
- Trophy points
- 6
- Location
- Turkey / Scotland
- Activity points
- 487
I saw this AC motor parameter calculator online: https://www.engineeringtoolbox.com/electrical-motor-calculator-d_832.html
It says for 100 Horse power, in 90% efficiency, 0.9 Power Factor and 220 V AC supply, 300A current is needed. But when I calculate like:
220V AC * 300 A AC * 0.707 (sine root mean sq) / 745.7 W (1 Horse power) = 56 HP
I get. Is my logic wrong?
Also, for a special purpose, I need to calculate the horsepower based on current flow in windings. In these windings below:
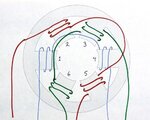
Because I only know my inductance(L) value, radius(R), turns(N) and RMS current which is going to flow through these winding coils. I know these below;
L = 60 mH
R = 5 cm
d(wire diameter) = 0.4 mm
N = 210
And RMS current for each phase (current flow on armature windings) is 12 A (peak to peak)
how can I calculate the horse power by only these parameters? Can I be sure that this parameters are whether enough or not enough to drive a car? Thanks.
It says for 100 Horse power, in 90% efficiency, 0.9 Power Factor and 220 V AC supply, 300A current is needed. But when I calculate like:
220V AC * 300 A AC * 0.707 (sine root mean sq) / 745.7 W (1 Horse power) = 56 HP
I get. Is my logic wrong?
Also, for a special purpose, I need to calculate the horsepower based on current flow in windings. In these windings below:
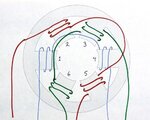
Because I only know my inductance(L) value, radius(R), turns(N) and RMS current which is going to flow through these winding coils. I know these below;
L = 60 mH
R = 5 cm
d(wire diameter) = 0.4 mm
N = 210
And RMS current for each phase (current flow on armature windings) is 12 A (peak to peak)
how can I calculate the horse power by only these parameters? Can I be sure that this parameters are whether enough or not enough to drive a car? Thanks.
Last edited: