JohnJohn20
Advanced Member level 4
Hi. I am using a RFP50N06 MOSFET to switch 24VDC into a DC motor which can draw up to 15 A. My test circuit was like this:
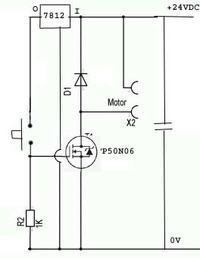
And this worked OK. However, when I increased the DC voltage to 32 V, it workrd for a bit and then the MOSFET shorted inside and wouldn't turn off.
Is it OK to directly connect 12VDC into the MOSFET gate like this? The datasheet says Vgs max of +-20V. Is current an issue here?
I am not sure what diode I have across the motor is. It is a rectifier I salvaged from a small power supply. Could that be an issue?
The MOSFET is mounted on a big heat sink that did not heat up at all.
Any suggestions as to why this happened would be appreciated.
John
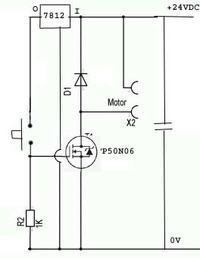
And this worked OK. However, when I increased the DC voltage to 32 V, it workrd for a bit and then the MOSFET shorted inside and wouldn't turn off.
Is it OK to directly connect 12VDC into the MOSFET gate like this? The datasheet says Vgs max of +-20V. Is current an issue here?
I am not sure what diode I have across the motor is. It is a rectifier I salvaged from a small power supply. Could that be an issue?
The MOSFET is mounted on a big heat sink that did not heat up at all.
Any suggestions as to why this happened would be appreciated.
John