randomshinichi
Newbie level 6
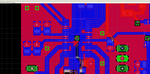
As you can see, EAGLE tells me that 24 needs to be connected to 28, which is connected to 29, which also connects to pin 31. Also, 10 needs to be connected to 8. (These are all ground)
The problem is, I already made vias between the ground planes on both sides of the board, but the airwires still show up (and you can see that there are no "islands" in the blue ground plane either). In other parts of the board EAGLE is smart enough to see that I have a via and the airwire disappears, but in this case they remain. Am I doing something wrong, or is EAGLE doing something wrong?
EDIT: FYI the green through-hole pin on the right marked "2" is the ground.