preethi19
Full Member level 5
Hi i am beginner in layout design and i am trying to design a layout for my circuit with reference to some examples i found. My doubt here is even if i follow the design rules for the contact what would be the correct way to place the contacts?? I know there is a minimum space, width rules that i need to follow. And in the image attached both the contacts on the poly follow the rules. Yet which is the better way to make the contact? Becoz in some examples i found the contact was just one and made big like the one below (but the poly length was less so the contact was bigger than the poly) and in some like 4 contacts together similar to the contact on the top poly in the image. If you say the above one is better could you also explain why. Is it just for the neatness of the design or is there any other factor to consider. Becoz in the end the contacts will be completely covered by the metal. Also say in above poly why do we have to use 2 contacts. Why cant i just use one on each poly and just make the connection. Thank you!!!
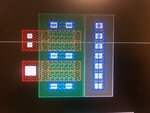
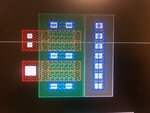
Last edited: