Kerrowman
Member level 4
- Joined
- Oct 12, 2021
- Messages
- 75
- Helped
- 0
- Reputation
- 0
- Reaction score
- 2
- Trophy points
- 8
- Location
- West Penwith
- Activity points
- 578
In my doing some research into the effects of HV CEMF pulses on batteries, I am finding that my MOSFETs understandably get easily damaged by these pulses, even when I have tried to isolate and protect them using a pair of chokes (see pic).
I also attach the relevant part of the circuit and wondered if anyone had any straightforward ideas as to how to block the CEMF pulses (~ 1,200V) from reaching the FETs? Maybe a fast diode between the Drain and Source of each one? However, the Source does not connect to Ground but supplies another part of the circuit.
Thanks
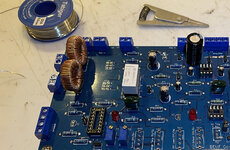
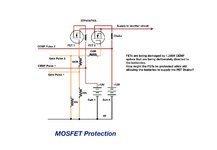
I also attach the relevant part of the circuit and wondered if anyone had any straightforward ideas as to how to block the CEMF pulses (~ 1,200V) from reaching the FETs? Maybe a fast diode between the Drain and Source of each one? However, the Source does not connect to Ground but supplies another part of the circuit.
Thanks
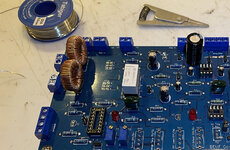
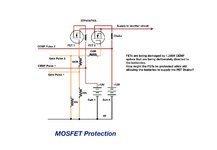