belax
Member level 2
Need help.
Need to design a dc/dc isolated voltage regulator.
Vin 60-160 v
Vout 5V
Io=0A - 5A
Efficiency more than 83 %.
The design should fit in 110x58x26 mm volume (aluminum box)
I started (draft design on paper) with flyback DCM topology.
1) ICE3BR0665J controller, 65 kHz, 0.65Ohm RDSon
2) VS-48CTQ060PbF output Schotky diode – the best in class with Vf=~0.5 voltage drop at 10A
3) Output caps before LC filter: 4pcs of Nichicon PW 1500 uF, 16V (1600 mA rms rated)
4) Transformer core EFD-25, Lprim=219 uH, turn ration n=Prim/Sec=10.5
My problems are:
1) I don’t know how to make the efficiency around 83 % staying in DCM and not using synchronous rectification.
2) To make output ripple current lower – because high ripple current makes me to use three caps before LC filter.
I attached my calcs.
I would like you (people) to check this calcs and give me advise how to minimize ripple current and increase efficiency of this flyback.
Thank you
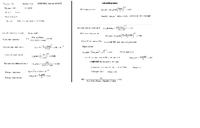
Need to design a dc/dc isolated voltage regulator.
Vin 60-160 v
Vout 5V
Io=0A - 5A
Efficiency more than 83 %.
The design should fit in 110x58x26 mm volume (aluminum box)
I started (draft design on paper) with flyback DCM topology.
1) ICE3BR0665J controller, 65 kHz, 0.65Ohm RDSon
2) VS-48CTQ060PbF output Schotky diode – the best in class with Vf=~0.5 voltage drop at 10A
3) Output caps before LC filter: 4pcs of Nichicon PW 1500 uF, 16V (1600 mA rms rated)
4) Transformer core EFD-25, Lprim=219 uH, turn ration n=Prim/Sec=10.5
My problems are:
1) I don’t know how to make the efficiency around 83 % staying in DCM and not using synchronous rectification.
2) To make output ripple current lower – because high ripple current makes me to use three caps before LC filter.
I attached my calcs.
I would like you (people) to check this calcs and give me advise how to minimize ripple current and increase efficiency of this flyback.
Thank you
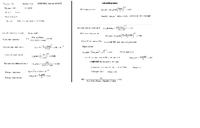