tonofsteel
Newbie level 4

- Joined
- May 21, 2013
- Messages
- 5
- Helped
- 0
- Reputation
- 0
- Reaction score
- 0
- Trophy points
- 1,281
- Activity points
- 1,409
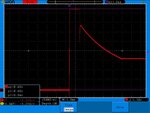
I am using a 3.3 Linear Regulator with a 16VDC supply. The regulator is a LD1086V33. I have powered development boards from this with no problems, BUT it will fry all the XBee's I connect to it. The attached image shows the waveform coming out of the regulator when power is connected. I have tried to measure this about 30 times now and about 1/3 of the time I will see a spike to 8 or 9 volts for 1-4ms before it goes down to 3.3V. The other times it will ramp to 3.3V with no spikes like in the attached image. The XBee will fail after two or three power-ups so I suspect that this voltage spike is wrecking them.
Is this common with all regulators? How do I protect against this? What are common ways of designing power regulator circuit protection for sensitive circuit supplies? I didn't think of checking this out until I had devices failing, is this situation common will all power supplies? If this is true then Digi did a poor job with robust product design.
I was thinking a zener or other diode to clip the voltage past a certain point.
Can a TVS be used for this? I remember seeing that most 3.3V TVS start to turn on above 9V and are made to protect against ESD so this wouldn't work in this case.
How do I build a regulator circuit to avoid these over voltages?