Hicham M
Member level 1

- Joined
- Feb 1, 2014
- Messages
- 38
- Helped
- 0
- Reputation
- 0
- Reaction score
- 0
- Trophy points
- 6
- Activity points
- 321
Hello guys,
I have 3G module in board and I want to replace it with a newer one.
The current module has BGA footprint with 188 pads, and the newer module i'm planning to use has an LGA (144 pad) footprint.
For prototyping, I was thinking to make a small board that will contain :
-on the top, the new module (in LGA footprint)
-on the bottom the current module BGA footprint to fit the place in the main board
and this small board will replace the current module (in BGA footprint)
Please, find an illustration of the my idea
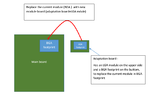
What do you think guys ? is this worth trying ?
I have 3G module in board and I want to replace it with a newer one.
The current module has BGA footprint with 188 pads, and the newer module i'm planning to use has an LGA (144 pad) footprint.
For prototyping, I was thinking to make a small board that will contain :
-on the top, the new module (in LGA footprint)
-on the bottom the current module BGA footprint to fit the place in the main board
and this small board will replace the current module (in BGA footprint)
Please, find an illustration of the my idea
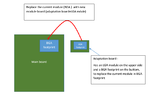
What do you think guys ? is this worth trying ?