netloginkk
Newbie level 5
- Joined
- May 7, 2010
- Messages
- 10
- Helped
- 0
- Reputation
- 0
- Reaction score
- 0
- Trophy points
- 1,281
- Location
- Hyderabad / Vizag
- Activity points
- 1,360
Hi,
I am testing IRF4905.
(Datasheet: http://www.irf.com/product-info/datasheets/data/irf4905.pdf )
For measuring RDS(ON), at VGS=-10 and ID=-38A, i have used the following circuit
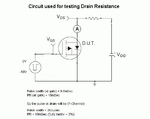
The drain resistor is a rheostat.
After applying pulsed gate voltage, i am varying VDD (10V to 30V) and the rheostat to get ID=38A (ammeter reads average, so 0.76A in ammeter is 38A peak (2% duty)).
Now i measure the drop between drain and source (VDS) using a DMM. so RDS(ON) = VDS/ID
I want to know whether this procedure to measure RDS(ON) is correct. The datasheet indicates a note at ID=-38A (pulsed current, 2% duty), but i managed it by switching gate. Do i need to keep the gate at -10V (constant) and apply a pulsed voltage to drain.
Could anyone suggest a better circuit or method.
I am testing IRF4905.
(Datasheet: http://www.irf.com/product-info/datasheets/data/irf4905.pdf )
For measuring RDS(ON), at VGS=-10 and ID=-38A, i have used the following circuit
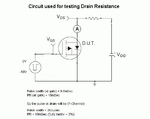
The drain resistor is a rheostat.
After applying pulsed gate voltage, i am varying VDD (10V to 30V) and the rheostat to get ID=38A (ammeter reads average, so 0.76A in ammeter is 38A peak (2% duty)).
Now i measure the drop between drain and source (VDS) using a DMM. so RDS(ON) = VDS/ID
I want to know whether this procedure to measure RDS(ON) is correct. The datasheet indicates a note at ID=-38A (pulsed current, 2% duty), but i managed it by switching gate. Do i need to keep the gate at -10V (constant) and apply a pulsed voltage to drain.
Could anyone suggest a better circuit or method.
Last edited by a moderator: