jovimon
Newbie level 6

HI: have a servomotor of about ½ hp (220), and want to turn it into a DC for a Eolic turbine application. I just have basics in electronics, and may be you could give a hand to wire it up for test it.
This motor comes from ZOJE SEWING MACHINE CO. Probably they are not the makers. They use it with their sewing machines. Down is the information I could gather. I´m including some pics that could help a little. It comes with two main cables: one with 4 leades (black, green, gray and brown), the second (Black, red, yellow, green and blue).
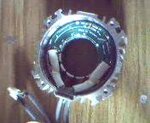
![Converted_file_7077646e[1].JPG Converted_file_7077646e[1].JPG](https://www.edaboard.com/data/attachments/35/35528-e4056df1fcb6da137e2d374f8599c90c.jpg)
It seems it manages nine diferent speeds
Model: PS-21
Voltage (AC) 220 V
Speed: 5500 RPM
Power: 380 W
Torque Moment: 1 N.M.
Working System: SI
Any help will be highly appreciated. Regards
This motor comes from ZOJE SEWING MACHINE CO. Probably they are not the makers. They use it with their sewing machines. Down is the information I could gather. I´m including some pics that could help a little. It comes with two main cables: one with 4 leades (black, green, gray and brown), the second (Black, red, yellow, green and blue).
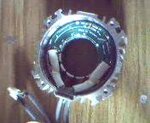
![Converted_file_7077646e[1].JPG Converted_file_7077646e[1].JPG](https://www.edaboard.com/data/attachments/35/35528-e4056df1fcb6da137e2d374f8599c90c.jpg)
It seems it manages nine diferent speeds
Model: PS-21
Voltage (AC) 220 V
Speed: 5500 RPM
Power: 380 W
Torque Moment: 1 N.M.
Working System: SI
Any help will be highly appreciated. Regards