911pcb
Junior Member level 1

- Joined
- Dec 6, 2010
- Messages
- 17
- Helped
- 0
- Reputation
- 0
- Reaction score
- 1
- Trophy points
- 1,283
- Activity points
- 1,828
911EDA provides PCB layout services to countries across the United States. Over the years, we have found that the industry is lacking a standard design process. So we have developed a standard process to take customers through PCB layouts in the most efficient manner. We suggest this process to every customer and it is generally accepted.
These are the usual steps to design a board for most customers that allow the customer maximum flexibility to make changes to embrace the normal engineering changes that happen during the design process. By utilizing this structured approach maximizes the engineering teams efforts to design and build a successful product.
1. Schematic / Components design review.
2. Determine what footprints are required to be built, and build them incorporating 3D models.
3. Board outline definition process. DXF board outline file import is the most stable method.
4. Component placement.
5. Customer review of component placement.
6. Power and Ground Plane assignment.
7. Customer review of Power Plane and Ground Plane Assignments.
8. Fanout.
9. Critical net routing.
10.Customer review of critical net routing.
11. Non critical net routing.
12. Customer review.
13. Silkscreen adjustment and board part number assignment/placement.
14. Gerber, DXF, Step, IDF/LDF final file generation for final customer review and approval.
15. Final cleanup and any touch up required from customer feedback.
If you are designing PCBs, try this process on your next project and let us know if it is helpful! If you have questions, please email me at ryano@911eda.com
Ryan O'Connor
911EDA, Inc.
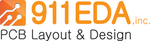
These are the usual steps to design a board for most customers that allow the customer maximum flexibility to make changes to embrace the normal engineering changes that happen during the design process. By utilizing this structured approach maximizes the engineering teams efforts to design and build a successful product.
1. Schematic / Components design review.
2. Determine what footprints are required to be built, and build them incorporating 3D models.
3. Board outline definition process. DXF board outline file import is the most stable method.
4. Component placement.
5. Customer review of component placement.
6. Power and Ground Plane assignment.
7. Customer review of Power Plane and Ground Plane Assignments.
8. Fanout.
9. Critical net routing.
10.Customer review of critical net routing.
11. Non critical net routing.
12. Customer review.
13. Silkscreen adjustment and board part number assignment/placement.
14. Gerber, DXF, Step, IDF/LDF final file generation for final customer review and approval.
15. Final cleanup and any touch up required from customer feedback.
If you are designing PCBs, try this process on your next project and let us know if it is helpful! If you have questions, please email me at ryano@911eda.com
Ryan O'Connor
911EDA, Inc.
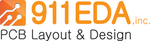