anotherbrick
Full Member level 4

- Joined
- Jan 10, 2009
- Messages
- 222
- Helped
- 1
- Reputation
- 2
- Reaction score
- 1
- Trophy points
- 1,298
- Location
- Istanbul , Turkey
- Activity points
- 3,190
hello dear forum
I want to add snubber to my mosfet H bridge
the DC link voltage is 300 VDC
and the H bridge circuit works as inverter producing 30 - 100 Hz alternating square wave
the values of components is not true I will use 100 nF and 1 K and UF4007
I want to ask if the following scheme is correct ?
thank you
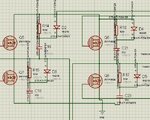
I want to add snubber to my mosfet H bridge
the DC link voltage is 300 VDC
and the H bridge circuit works as inverter producing 30 - 100 Hz alternating square wave
the values of components is not true I will use 100 nF and 1 K and UF4007
I want to ask if the following scheme is correct ?
thank you
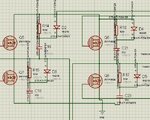