elecTomas
Junior Member level 2

Dear all,
I am designing the control loop of a 3 stages interleaved boost converter already built and operating. However, the inner current loop gives a current value which is two times what I expect. The small-signal model and transfer functions are correct, they have been checked several times by different people already and also compared with other papers and researches. Let me briefly explain the design of the model.
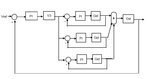
There are three inner loops for the current control, one loop for each inductor, where the reference is the input current divided by three. Gid is the control-to-inductor current transfer function. The outer loop corresponds to the voltage control, Gvi is the input current-to-output voltage transfer function. The output voltage follows perfectly the reference, but the current is two times what I expect, exactly two times.
I have also tried by simplifying the model to single-stage boost converter, and the result is exactly the same. And as I have said, the transfer functions are correctly calculated.
Thanks a lot for your help.
I am designing the control loop of a 3 stages interleaved boost converter already built and operating. However, the inner current loop gives a current value which is two times what I expect. The small-signal model and transfer functions are correct, they have been checked several times by different people already and also compared with other papers and researches. Let me briefly explain the design of the model.
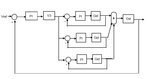
There are three inner loops for the current control, one loop for each inductor, where the reference is the input current divided by three. Gid is the control-to-inductor current transfer function. The outer loop corresponds to the voltage control, Gvi is the input current-to-output voltage transfer function. The output voltage follows perfectly the reference, but the current is two times what I expect, exactly two times.
I have also tried by simplifying the model to single-stage boost converter, and the result is exactly the same. And as I have said, the transfer functions are correctly calculated.
Thanks a lot for your help.