hshah8970
Full Member level 2
Hello! This is a circuit for a motor being driven by an opamp. I do not understand the purpose of the C1 in there. Is it some sort of external compensation for the inductive load (motor) ?
Also, if you can, please tell me what a linear power opamp is? I mean what would a non-linear power opamp mean?
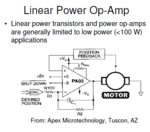
Also, if you can, please tell me what a linear power opamp is? I mean what would a non-linear power opamp mean?
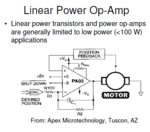