haohaodk46
Member level 4
Hi All,
I have a RS485 network with 32 nodes
This is my circuit
This issue here is My board some days is burn some component on board
I use switching power supply like this to supply 24V for all nodes on bus
And Here is picture components is burned
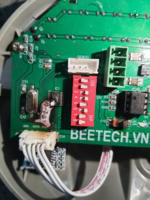
on The bus have 32 nodes but just have 1 or 2 boards is burned.
And maybe about some days the other board is burn
There is any component is shorted and cause burn or over volatage 24V on board ?
Every one have explain why ? Help me !!!!
Thanks
I have a RS485 network with 32 nodes
This is my circuit
This issue here is My board some days is burn some component on board
I use switching power supply like this to supply 24V for all nodes on bus
And Here is picture components is burned
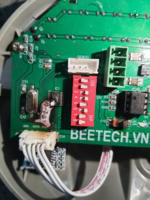
on The bus have 32 nodes but just have 1 or 2 boards is burned.
And maybe about some days the other board is burn
There is any component is shorted and cause burn or over volatage 24V on board ?
Every one have explain why ? Help me !!!!
Thanks
Last edited by a moderator: