Nicx
Junior Member level 1
hi, ive been trying to construct a buck converter with output 24V and 10A max. but i would settle for about 150Watts output. my input specs are 30V minimum and 60V max.
when i tried testing it at constant voltage test of an e-load, the current output registered on the e-load is almost the same as the current drawn from the supply. i'm currently testing it with a desktop DC power supply with output 30V-3A. and since my circuit is acting this way, my max power is about 72Watts. i was advised to place two of these DC power supplies in series so i would get the 60V max input and 180Watts of total power input. however when i hooked it up to my circuit, and ran a constant voltage test, my circuit got fried. specifically the pwm controller's Vcc resistor.
can someone suggest how i should debug this? how do i fix the load=supply current problem? my calculations indicate an inductance of 18uH and ive increased mine to 39uH to avoid saturation. im using an iron powder toroid core for the inductor (material -26). ive attached a schematic. i need help badly please. thanks!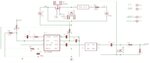
when i tried testing it at constant voltage test of an e-load, the current output registered on the e-load is almost the same as the current drawn from the supply. i'm currently testing it with a desktop DC power supply with output 30V-3A. and since my circuit is acting this way, my max power is about 72Watts. i was advised to place two of these DC power supplies in series so i would get the 60V max input and 180Watts of total power input. however when i hooked it up to my circuit, and ran a constant voltage test, my circuit got fried. specifically the pwm controller's Vcc resistor.
can someone suggest how i should debug this? how do i fix the load=supply current problem? my calculations indicate an inductance of 18uH and ive increased mine to 39uH to avoid saturation. im using an iron powder toroid core for the inductor (material -26). ive attached a schematic. i need help badly please. thanks!
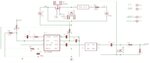