yokohama
Member level 3

Hi everybody,
I would to drive a solenoid with a mosfet and measuring the current by adding a 0.1 Ohm resistor between the source of the mosfet and the GND. (See the schematic below).
When probing this point with a scope I see this signal (see scope capture below). What I would, is cleaning this signal before sending it to the ADC for a correct reading.
I have tried to do that by adding a LC circuit but the result is poor. Can you please suggest me some solutions.
Thank's.
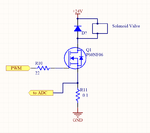
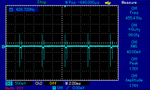
I would to drive a solenoid with a mosfet and measuring the current by adding a 0.1 Ohm resistor between the source of the mosfet and the GND. (See the schematic below).
When probing this point with a scope I see this signal (see scope capture below). What I would, is cleaning this signal before sending it to the ADC for a correct reading.
I have tried to do that by adding a LC circuit but the result is poor. Can you please suggest me some solutions.
Thank's.
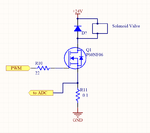
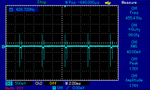