drkirkby
Full Member level 6
I've put some background information to my problem. If you don't want to read that, just skip the section marked "Background" and go directly to the section marked "HFSS problem".
Background.
I purchased cheaply an HP 16453A Dielectric Material Test Fixture. A picture of which is shown.
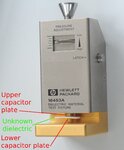
It is designed to allow one to determine the complex permittivity of a dielectric, by inserting the dielectric between two capacitor plate, and measuring the impedance.
An HP/Agilent/Keysight 16453A Dielectric Material Test Fixture, used in conjunction with a limited range HP/Agilent/Keysight instruments:
Er=Er' + j Er''
by converting measurements of impedance (R + j X) to permittivity. This requires 4 things:
I don't have any of those instruments, but I do have other instruments able to measure impedance. But these instruments don't have the necessary firmware support to convert the R + j X values to Er' + Er''. I want to use one of my instruments, despite they don't have the right firmware, as they do have the basic measurement capability to measure R + j X.
HFSS problem
Can anyone help me set up a simulation in HFSS, where from these inputs
HFSS is able to compute R + j X?
If I can compute R + j X with a number of different dielectric thicknesses, and complex permittivities, I'm sure I could create a lookup table or empirical equation to work the other way, and convert measured values of thickness, and complex impedance into complex permittivity.
I'm really now sure
Can anyone help?
Dave
Background.
I purchased cheaply an HP 16453A Dielectric Material Test Fixture. A picture of which is shown.
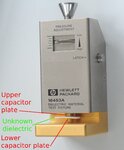
It is designed to allow one to determine the complex permittivity of a dielectric, by inserting the dielectric between two capacitor plate, and measuring the impedance.
An HP/Agilent/Keysight 16453A Dielectric Material Test Fixture, used in conjunction with a limited range HP/Agilent/Keysight instruments:
- HP 4291A RF Impedance/Material Analyzer (Obsolete)
- HP 4291B RF Impedance/Material Analyzer (Obsolete)
- Agilent/Keysight E4991A (Discontinued, but currently supported)
- Agilent.Keysight E4991B Impedance Analyzer, 1MHz to 500 MHz/1 GHz/3 GHz (A current product selling at US$38,221)
Er=Er' + j Er''
by converting measurements of impedance (R + j X) to permittivity. This requires 4 things:
- A flat material with a thickness in the range 0.3 to 3.0 mm and a diameter of at least 15 mm.
- Measurement of the thickness of the material with a micrometer.
- Measurement of R + j X on the impedance analyzer.
- Firmware support in the impedance analyzer to convert those R+j X values to Er' + j Er'' - that alone is over $5000 on the only current one of these instruments.
I don't have any of those instruments, but I do have other instruments able to measure impedance. But these instruments don't have the necessary firmware support to convert the R + j X values to Er' + Er''. I want to use one of my instruments, despite they don't have the right firmware, as they do have the basic measurement capability to measure R + j X.
HFSS problem
Can anyone help me set up a simulation in HFSS, where from these inputs
- Diameter of the smaller capacitor plate is 7 mm
- Diameter of larger capacitor plate is 10 mm
- A known thickness of dielectric, which will be in the range 0.3 to 3.0 mm. The dielectric must be flat - unlike in my photo.
- A known complex permittivity of the dielectric
- A dielectric at least 15 mm in diameter - I assume this means fringing fields around the edges of the dielectric are negligible
HFSS is able to compute R + j X?
If I can compute R + j X with a number of different dielectric thicknesses, and complex permittivities, I'm sure I could create a lookup table or empirical equation to work the other way, and convert measured values of thickness, and complex impedance into complex permittivity.
I'm really now sure
- How I can compute R + j X of a capacitor.
- How to determine an appropriate criteria for convergence, since I suspect that the default will not be suitable
Can anyone help?
Dave