yoosefheidari
Member level 5
hi everyone
idesign this circuit to bosst voltage from 15v to 36v
in no load condition everything is ok and output voltage is 36v but when i put 7 ohm load in output voltage drop to about 15.5 volt and current about 2.5 amp.
where is problem?why voltage drop from 36 volt to 15.5 under load?
i add 56k resistor beetwen pin3 & pin4 for slope compensation.
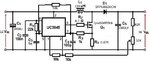
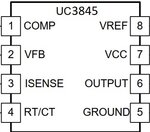
idesign this circuit to bosst voltage from 15v to 36v
in no load condition everything is ok and output voltage is 36v but when i put 7 ohm load in output voltage drop to about 15.5 volt and current about 2.5 amp.
where is problem?why voltage drop from 36 volt to 15.5 under load?
i add 56k resistor beetwen pin3 & pin4 for slope compensation.
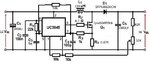
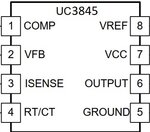