deepak4you
Member level 1
Another shout for help to the experts.
What I have:
1. Two machines driven by two ICE Engines. Both have onboard alternators that is used for ignition and charging the battery as in any vehicle.
2. Engine 1 is a smaller one that has a 12V equivalent alternator #1. Output current is in the range of 8-9 amps. Generally is running all the time
3. Engine 2 is the bigger one that has a 48V equivalent alternator #2. Output current is in the range of about 10-18 amps. This one is running on-and-off
4. Both engines run at varying rpm depending on the load, hence their respective alternators also have varying outputs within their operating range
What I intend to do:
There is some power demand for other tasks on the shop floor. I intend to install an appropriate AC Inverter (approx 4kW)to cater to that demand. Only difference that I intend to use a huge bank of used LFP lithium battery packs in a 19SXP/60V configuration. These batteries are used and lower capacity, but still better able to deliver enough juice for the inverter and load.
How I intend to do what I intend to do:
1. Since both engines are running, I tap both the alternators, feed the output into a buck-boost converter.
2. Output of the buck-boost converter feeds the BMS for the Li Battery pack to charge the battery pack
My problem:
1. Engine 1 is running all the time - Li batteries can all be charging as long as Engine 1 is running, albeit at a lot lower charge rate since Alternator 1 is at 12V while the output of the buck-boost would be approx 65V. Increase in voltage, loss in current
2. Engine 2/Alternator 2 on the other hand has a higher voltage and current, but not running all the time. I'm trying to see if I can feed the output of Alternator 2 also to Buck-Boost converter so that I get lot more voltage and current to charge the Li battery pack quicker.
I read up and I understand that we can add two voltage sources in series as input to an SMPS. Of my limited understanding, a buck-boost converter is also essentially an SMPS. If that indeed is the case, would the attached configuration work? Or is there a better way of achieving what I intend to do?
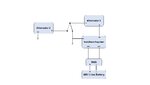
Regards,
Deepak
What I have:
1. Two machines driven by two ICE Engines. Both have onboard alternators that is used for ignition and charging the battery as in any vehicle.
2. Engine 1 is a smaller one that has a 12V equivalent alternator #1. Output current is in the range of 8-9 amps. Generally is running all the time
3. Engine 2 is the bigger one that has a 48V equivalent alternator #2. Output current is in the range of about 10-18 amps. This one is running on-and-off
4. Both engines run at varying rpm depending on the load, hence their respective alternators also have varying outputs within their operating range
What I intend to do:
There is some power demand for other tasks on the shop floor. I intend to install an appropriate AC Inverter (approx 4kW)to cater to that demand. Only difference that I intend to use a huge bank of used LFP lithium battery packs in a 19SXP/60V configuration. These batteries are used and lower capacity, but still better able to deliver enough juice for the inverter and load.
How I intend to do what I intend to do:
1. Since both engines are running, I tap both the alternators, feed the output into a buck-boost converter.
2. Output of the buck-boost converter feeds the BMS for the Li Battery pack to charge the battery pack
My problem:
1. Engine 1 is running all the time - Li batteries can all be charging as long as Engine 1 is running, albeit at a lot lower charge rate since Alternator 1 is at 12V while the output of the buck-boost would be approx 65V. Increase in voltage, loss in current
2. Engine 2/Alternator 2 on the other hand has a higher voltage and current, but not running all the time. I'm trying to see if I can feed the output of Alternator 2 also to Buck-Boost converter so that I get lot more voltage and current to charge the Li battery pack quicker.
I read up and I understand that we can add two voltage sources in series as input to an SMPS. Of my limited understanding, a buck-boost converter is also essentially an SMPS. If that indeed is the case, would the attached configuration work? Or is there a better way of achieving what I intend to do?
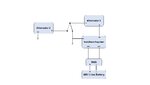
Regards,
Deepak