Gilligan8
Newbie level 4
I have a conveyor dryer for screen printing and it has 3 heater panels that are wired in parallel to a distro block.
They are 220v drawing about 12+ amps. One of these has a temp probe in it and has a readout on my panel. The problem is that if one of the other 2 go out, I have no way of knowing and it can really ruin a job and not cure the shirts properly. Right now the only way I can tell is I check to make sure the panels are heating up (by touching) when I start the dryer up. Then after I'm done with a job I shoot the panels with a infrared temp gun to make sure they are still hot. Not really ideal at all.
So, my idea is to drive some LED's off the leads going to each panel via a toroidal transformer. I will at least see if they all light up together while they panels are in their on cycle (obviously they cycle to stay at X temp) or if one of them has failed.
So as a proof of concept I grabbed a clip on core and wrapped a bit of solid core telephone cable and wrapped it. I then clipped it on a lead and turned it on then checked for voltage with my fieldpiece meter (granted kind of crude, possibly only measures down to a 10th of a volt)... but I got ZILCH... not even .1v.
Here is a pic of my admittedly VERY week proof of concept transformer.
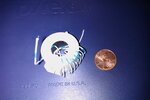
Am I just not putting enough into the windings or am I barking up the wrong tree entirely?
They are 220v drawing about 12+ amps. One of these has a temp probe in it and has a readout on my panel. The problem is that if one of the other 2 go out, I have no way of knowing and it can really ruin a job and not cure the shirts properly. Right now the only way I can tell is I check to make sure the panels are heating up (by touching) when I start the dryer up. Then after I'm done with a job I shoot the panels with a infrared temp gun to make sure they are still hot. Not really ideal at all.
So, my idea is to drive some LED's off the leads going to each panel via a toroidal transformer. I will at least see if they all light up together while they panels are in their on cycle (obviously they cycle to stay at X temp) or if one of them has failed.
So as a proof of concept I grabbed a clip on core and wrapped a bit of solid core telephone cable and wrapped it. I then clipped it on a lead and turned it on then checked for voltage with my fieldpiece meter (granted kind of crude, possibly only measures down to a 10th of a volt)... but I got ZILCH... not even .1v.
Here is a pic of my admittedly VERY week proof of concept transformer.
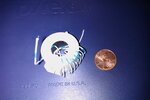
Am I just not putting enough into the windings or am I barking up the wrong tree entirely?