kathmandu
Full Member level 5
Hello,
I'm in the process of building a sine wave inverter (Mosfet full-bridge and a low freq transformer).
Anyway, I don't manage to tune up the output filter (a series inductor in the transformer primary circuit and a capacitor across transformer secondary).
I have tried different inductor cores (E shape ferrite, ferromagnetic toroid) but the output voltage isn't perfect (there are some perturbations around the middle point of every half wave - between the zero crossing and peak voltage).
This is happening at no load or with a small resistive load (60W bulb lamp).When I connect an AC fan (150W), the output is clipping harder (the wave form has almost a trapezoid shape) and the transformer starts humming.
The inverter is rated at + 1000 W (24 V DC link, 170 Amp Mosfets, 1000 W toroidal transformer). The clipping is not caused by low voltage DC-link (the battery bank is oversized too).
What could be the problem? What's the effect of a bigger/smaller filter inductance or capacitor? Thank you very much for your help.
I've attached some oscilloscope printscreens:
(1) - output voltage at no load (or small resistive load)
**broken link removed**
**broken link removed**
(2) - output voltage for an inductive load (400W corded power drill)
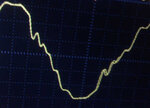
Does anyone have any clue about what's happening?
I'm in the process of building a sine wave inverter (Mosfet full-bridge and a low freq transformer).
Anyway, I don't manage to tune up the output filter (a series inductor in the transformer primary circuit and a capacitor across transformer secondary).
I have tried different inductor cores (E shape ferrite, ferromagnetic toroid) but the output voltage isn't perfect (there are some perturbations around the middle point of every half wave - between the zero crossing and peak voltage).
This is happening at no load or with a small resistive load (60W bulb lamp).When I connect an AC fan (150W), the output is clipping harder (the wave form has almost a trapezoid shape) and the transformer starts humming.
The inverter is rated at + 1000 W (24 V DC link, 170 Amp Mosfets, 1000 W toroidal transformer). The clipping is not caused by low voltage DC-link (the battery bank is oversized too).
What could be the problem? What's the effect of a bigger/smaller filter inductance or capacitor? Thank you very much for your help.
I've attached some oscilloscope printscreens:
(1) - output voltage at no load (or small resistive load)
**broken link removed**
**broken link removed**
(2) - output voltage for an inductive load (400W corded power drill)
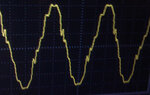
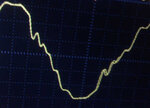
Does anyone have any clue about what's happening?