mmitchell
Advanced Member level 4
Hi,
In IPC-2221, 6.3, Table 6-1 Electrical Conductor Spacing I encountered the concept of conformal coating. In this table, conductor coating are classified into two types:
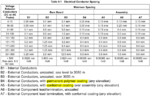
After reading materials at
[1] Conformal coating - Wikipedia, the free encyclopedia
[2] Dow Corning - What are Conformal Coatings?
It seems that the key characteristics of conforming is that
I have only used solder mask before. Solder mask is for preventing solder from bridging pins, and it is applied before soldering, so it seems that it can easily be distinguished from conformal coating.
But is solder mask the same concept as (1) permanent polymer coating? Should I use columns corresponding to (1) for determining conductor spacing?
Matt
In IPC-2221, 6.3, Table 6-1 Electrical Conductor Spacing I encountered the concept of conformal coating. In this table, conductor coating are classified into two types:
- Permanent polymer coating
- Conformal coating
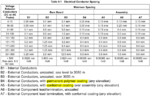
After reading materials at
[1] Conformal coating - Wikipedia, the free encyclopedia
[2] Dow Corning - What are Conformal Coatings?
It seems that the key characteristics of conforming is that
- It is applied after all components have been soldered.
- Its primary purpose is for providing an additional covering layer to withstand harsh environments, such as high humidity.
I have only used solder mask before. Solder mask is for preventing solder from bridging pins, and it is applied before soldering, so it seems that it can easily be distinguished from conformal coating.
But is solder mask the same concept as (1) permanent polymer coating? Should I use columns corresponding to (1) for determining conductor spacing?
Matt