Malonga
Newbie level 4
Hi all,
I am new here so I hope I am posting in the right place.
I am currently working on a uni design project and need some help. The project involves designing and making a circuit which will drive a small motor forwards or backwards depending on the temperature.
This is my design so far,
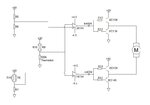
I have decided to use a pair of op amps as comparators with the thermistor being common between the two. The idea is then that the op amps will out put a positive signal when the temperature either goes above or below set temperatures.
This signal from the op amp will then trigger the H bridge to either run the motor forward or in reverse.
I am hoping that someone will be able to have a quick look over what I am planning on doing and tell me if I am going in the right direction. This is my first year at uni and I haven't had a lot of experience with electronics so I am expecting to make a few mistakes along the way.
Cheers,
Craig
I am new here so I hope I am posting in the right place.
I am currently working on a uni design project and need some help. The project involves designing and making a circuit which will drive a small motor forwards or backwards depending on the temperature.
This is my design so far,
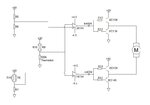
I have decided to use a pair of op amps as comparators with the thermistor being common between the two. The idea is then that the op amps will out put a positive signal when the temperature either goes above or below set temperatures.
This signal from the op amp will then trigger the H bridge to either run the motor forward or in reverse.
I am hoping that someone will be able to have a quick look over what I am planning on doing and tell me if I am going in the right direction. This is my first year at uni and I haven't had a lot of experience with electronics so I am expecting to make a few mistakes along the way.
Cheers,
Craig