MD_SHAHRUKH
Advanced Member level 4
- Joined
- Jun 5, 2017
- Messages
- 103
- Helped
- 4
- Reputation
- 8
- Reaction score
- 5
- Trophy points
- 18
- Location
- Bangalore, India
- Activity points
- 1,107
Hello everyone,
I am a student and currently doing a project. My project is Implementation of CAN bus in industry . Here I want to know about the advantages of CAN bus over other industrial bus such as profi bus and foundation field bus. If CAN is so efficient in automobile then why it is not used in industries. And what problems can occur if CAN is implemented in industry automation or disadvantage of CAN in industrial automation.
I have a block diagram which I have made to make my project.
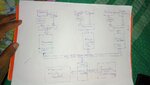
I am a student and currently doing a project. My project is Implementation of CAN bus in industry . Here I want to know about the advantages of CAN bus over other industrial bus such as profi bus and foundation field bus. If CAN is so efficient in automobile then why it is not used in industries. And what problems can occur if CAN is implemented in industry automation or disadvantage of CAN in industrial automation.
I have a block diagram which I have made to make my project.
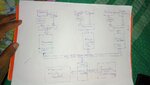