3BABY
Member level 5
- Joined
- Jan 14, 2011
- Messages
- 91
- Helped
- 0
- Reputation
- 0
- Reaction score
- 0
- Trophy points
- 1,286
- Location
- New Zealand
- Activity points
- 2,252
Hi Guys,
Im having a bit of trouble with a circuit. Please see schematic below. the top portion is a Capacitor Discharge Ignition circuit using a SCR, this is triggered by a microcontroller (not in schematic), the second portion is a 150-250V DC generator using a Step-Up DC-DC Controller (using the MAX1771) which was basically the same circuit as this Nixie tube HV generatoe
The Problem i have is i dont think the MAX1771 generator circuit can supply enough energy to the charge the capacitor, as far as im aware (after building the circuit) the 1uF capacitor would require approximately 1A at around 200V for 350uS. At the moment when i power on the system with a test program generating periodic 1mS (ON --> trigger SCR) pulses and 50mS apart this causes (Using OPTION 2 on the schematic, a direct connection from HV generator to CDI circuit (please see schematic)) the inductor of the MAX1771 circuit to breakdown and i end up with a fried inductor. If i use OPTION 1, a resistor in between the HV generator and the CDI circuit the resistor ends up getting fried.
So my question is: if i need to think about a different design for my high voltage generator, a design that can deliver approx 1A@ 200V DC in 350uS can anyone suggest a circuit? whether is be a DC-boost type or even a transformer.
Before anyone points out, yes most engines using CDI ignition have a HV generator coil for this purpose, i would not like to use this approach as this relies on engine RPM to generate a decent spark. i would like a stand alone HV generator to deliver sufficient spark energy at any RPM.
Periodic 1mS pulse to trigger SCR:

Schematic of current System:
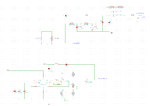
Any Help would be much appreciated!
Im having a bit of trouble with a circuit. Please see schematic below. the top portion is a Capacitor Discharge Ignition circuit using a SCR, this is triggered by a microcontroller (not in schematic), the second portion is a 150-250V DC generator using a Step-Up DC-DC Controller (using the MAX1771) which was basically the same circuit as this Nixie tube HV generatoe
The Problem i have is i dont think the MAX1771 generator circuit can supply enough energy to the charge the capacitor, as far as im aware (after building the circuit) the 1uF capacitor would require approximately 1A at around 200V for 350uS. At the moment when i power on the system with a test program generating periodic 1mS (ON --> trigger SCR) pulses and 50mS apart this causes (Using OPTION 2 on the schematic, a direct connection from HV generator to CDI circuit (please see schematic)) the inductor of the MAX1771 circuit to breakdown and i end up with a fried inductor. If i use OPTION 1, a resistor in between the HV generator and the CDI circuit the resistor ends up getting fried.
So my question is: if i need to think about a different design for my high voltage generator, a design that can deliver approx 1A@ 200V DC in 350uS can anyone suggest a circuit? whether is be a DC-boost type or even a transformer.
Before anyone points out, yes most engines using CDI ignition have a HV generator coil for this purpose, i would not like to use this approach as this relies on engine RPM to generate a decent spark. i would like a stand alone HV generator to deliver sufficient spark energy at any RPM.
Periodic 1mS pulse to trigger SCR:

Schematic of current System:
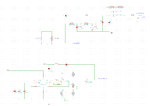
Any Help would be much appreciated!