mrinalmani
Advanced Member level 1
- Joined
- Oct 7, 2011
- Messages
- 463
- Helped
- 60
- Reputation
- 121
- Reaction score
- 58
- Trophy points
- 1,318
- Location
- Delhi, India
- Activity points
- 5,285
Hi
I have a 12V full bridge operating at 100KHz, driving a transformer. The transformer output is rectified and filtered with a capacitor and then connected to a resistive load.
The 12V input to the bridge comes form a pair of 1.5 meter long copper cable, 4mm in diameter.
The rail voltage is very unstable. The pk-pk ripple is roughly 5V at 40A current, with 50uF ceramic capacitors connected across the rails.
Connecting additional 7000uF aluminium capacitor lowers the ripple to 3V pk-pk. The capacitor begins to heat up.
Adding another 14000uF lowers the ripple only by 0.5V. It appears that the value of ripple is more dependent on the NUMBER of capacitors in parallel rather than the value of the capacitors.
I am doubting the lead inductance to be the culprit.
The figure shows the position of the capacitors marked in red.
(The connecting cables are just for illustration, and not of actual capacity)
How to stabilize the rail voltage of the bridge?
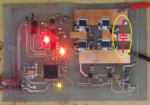
Thank you
I have a 12V full bridge operating at 100KHz, driving a transformer. The transformer output is rectified and filtered with a capacitor and then connected to a resistive load.
The 12V input to the bridge comes form a pair of 1.5 meter long copper cable, 4mm in diameter.
The rail voltage is very unstable. The pk-pk ripple is roughly 5V at 40A current, with 50uF ceramic capacitors connected across the rails.
Connecting additional 7000uF aluminium capacitor lowers the ripple to 3V pk-pk. The capacitor begins to heat up.
Adding another 14000uF lowers the ripple only by 0.5V. It appears that the value of ripple is more dependent on the NUMBER of capacitors in parallel rather than the value of the capacitors.
I am doubting the lead inductance to be the culprit.
The figure shows the position of the capacitors marked in red.
(The connecting cables are just for illustration, and not of actual capacity)
How to stabilize the rail voltage of the bridge?
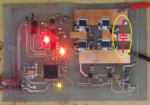
Thank you