franticEB
Full Member level 3
Hi,
i'm designing an isolated DCM flyback with this feature:
Vin_min=36Vdc
Vin_nom=48Vdc
Vout_max=63Vdc
Vout=250V
Iout=0.2A
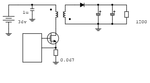
At the moment the problems are on transformer windings.
The transformer i've made is RM8 N87 gapped AL 250nH with 10 turns of primary (AWG 21 equivalent litz wire) and 86 turns of secondary (AWG 26).
The secondary winding goes to 90° after 3 minutes since startup.
I did not expect this increase in temperature from the calculations I had done.
Could you help me in understanding this fact?
Thanks
i'm designing an isolated DCM flyback with this feature:
Vin_min=36Vdc
Vin_nom=48Vdc
Vout_max=63Vdc
Vout=250V
Iout=0.2A
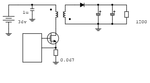
At the moment the problems are on transformer windings.
The transformer i've made is RM8 N87 gapped AL 250nH with 10 turns of primary (AWG 21 equivalent litz wire) and 86 turns of secondary (AWG 26).
The secondary winding goes to 90° after 3 minutes since startup.
I did not expect this increase in temperature from the calculations I had done.
Could you help me in understanding this fact?
Thanks