DesertEagle
Newbie level 5
Hy,
if searched this forum for quite a while but I can't get a clue what is wrong with my circuit. I have following problem:
I have two strain gauges mounted on a beam connected to a soldering pad with two 120Ohm precision resistors. The strain gauges and the resistors are aranged as a Wheathstone bridge and connected to 5V supply, GND and to an Amplifier for the output signal.
At the beginning (beam unloaded) I have quite huge offset voltages of around 3 to 4mV (without the gain). I tried now to put a poti in paralell to the bridge as shown in many application guides to zero the bridge.
Without the Poti, the arrangement deliveres stable signals. As soon as the poti is installed, the signal shown huge fluctuation (after the amplifier).
The poti is installed at the end of the cable connection (apprx. 4m cable inbetween) since the arrangement is not accessible at the point where the bridge is installed (see attachment for details).
Does anybody have an idea where this fluctuation may arise from? Is the Poti creating a loop which causes the fluctuations?
Any help is highly appreciated :thumbsup:
Regards,
Dan
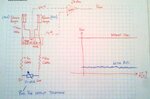
if searched this forum for quite a while but I can't get a clue what is wrong with my circuit. I have following problem:
I have two strain gauges mounted on a beam connected to a soldering pad with two 120Ohm precision resistors. The strain gauges and the resistors are aranged as a Wheathstone bridge and connected to 5V supply, GND and to an Amplifier for the output signal.
At the beginning (beam unloaded) I have quite huge offset voltages of around 3 to 4mV (without the gain). I tried now to put a poti in paralell to the bridge as shown in many application guides to zero the bridge.
Without the Poti, the arrangement deliveres stable signals. As soon as the poti is installed, the signal shown huge fluctuation (after the amplifier).
The poti is installed at the end of the cable connection (apprx. 4m cable inbetween) since the arrangement is not accessible at the point where the bridge is installed (see attachment for details).
Does anybody have an idea where this fluctuation may arise from? Is the Poti creating a loop which causes the fluctuations?
Any help is highly appreciated :thumbsup:
Regards,
Dan
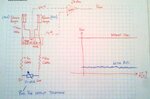