mmitchell
Advanced Member level 4
Hi,
In IPC-7351, table 3-4 to table 3-14 contain the defined “courtyard excess” for placement density level A, B and C. According to Note 3 on page 1, definitions in this IPC-7351 standard are for reflow soldering.
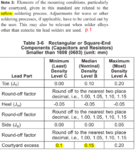
In prototyping however, can I ask a solderer to solder level C spacing board?
Take capacitors and resistors for example. By table 3-6, “courtyard excess”
If one chooses level C, the minimum pad spacing between different components (capacitors, resistors, and pads of other ICs) is 2x courtyard excess = 0.1 × 2 = 0.2mm = 7.874mil.
There would be solder mask between them with the usual solder mask expansion is between 0 and 5 mil. If we assume 0mil for minimum so that we get 7.874mil solder mask separating the two close pads exactly, then can it guarantee no bridging would occur? From the perspective of solder mask width this is enough; but isn’t the pad spacing too small? Can any solderer work with that?
On the other hand, if I adopt level A spacing in prototype board so that 2x courtyard excess = 0.2 × 2 = 0.4mm = 15.748mil, two times of that for level C, is it spacing large enough for solderers to handle manually?
Matt
In IPC-7351, table 3-4 to table 3-14 contain the defined “courtyard excess” for placement density level A, B and C. According to Note 3 on page 1, definitions in this IPC-7351 standard are for reflow soldering.
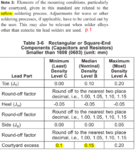
In prototyping however, can I ask a solderer to solder level C spacing board?
Take capacitors and resistors for example. By table 3-6, “courtyard excess”
- Level C: 0.1mm
- Level B: 0.15mm
- Level A: 0.20mm
If one chooses level C, the minimum pad spacing between different components (capacitors, resistors, and pads of other ICs) is 2x courtyard excess = 0.1 × 2 = 0.2mm = 7.874mil.
There would be solder mask between them with the usual solder mask expansion is between 0 and 5 mil. If we assume 0mil for minimum so that we get 7.874mil solder mask separating the two close pads exactly, then can it guarantee no bridging would occur? From the perspective of solder mask width this is enough; but isn’t the pad spacing too small? Can any solderer work with that?
On the other hand, if I adopt level A spacing in prototype board so that 2x courtyard excess = 0.2 × 2 = 0.4mm = 15.748mil, two times of that for level C, is it spacing large enough for solderers to handle manually?
Matt