doncarlosalbatros
Full Member level 2
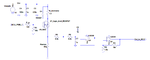
This question is about a personal project and related to my previous question but focusing on different issues or questions. Heating wire is 1.9 ohm but I can adjust it to obtain 6A current pulse amplitude.
A uC's PWM output will control 2A to 6A current through a heating-wire and since the resistance might change, the current value roughly will be fed back to ADC of the uC for regulation ect. The circuit will be soldered on a perfboard.
I decided to use a single-supply op amp and low-side sensing to avoid common-mode-voltage related issues.
The freq. of the uC PWM is 500Hz and the PWM pulses are 0/5V . Here is the datasheet of the MOSFET: **broken link removed**
Here is how Im planning to wire it:
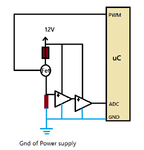
And here is the power dissipation of the MOSFET at %95 PWM(you can see the peak and average power):
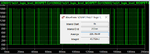
I asked this to some and forums and some say I dont need any driver for the FET at this freq. and voltage.
My questions are do I need to worry about a driver for the MOSFET? Do I need heat.sink?
Is 50m Ohm resistor good for this application?
And what type of capacitors should I use for the active filter's 1uF caps?
If I go lower resistor than the input offset voltage becomes an issue. Is there a better rail-rail single supply opamp for a lower input offset voltage? I tried such in LTspice but getting worse results for the active filter.