neazoi
Advanced Member level 6
Hello,
I have an adsl router at home (like most) and a small computer (mini server) connected to it.
The computer is an Alix-1D and consumes only 5W max at 12V.
I want to build a small UPS for these two, so that it can keep them up and running when power is lost. Mostly interested in sudden power loss, a few minutes max (which happens oftenly) and not long time power loss. Note, only 12v DC output is needed, not conversion to 220v AC.
I want to use 10 low self discharge AA NiMH batteries connected in series to produce about 12v, just what the computer and the router needs.
A simple UPS can be as simple as this one
with two diodes.
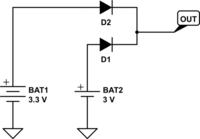
However this does not charge the batteries, so I need a circuit to charge these 10 NiMH batteries connected in series. I need this circuit to be safe, not exploding the batteries, as it is for home use. So something like this
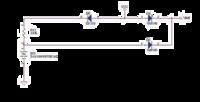
[found at www .electronics -circuits .com /schematics /embedded /battery -backup .png[/url]
is not good probably as will overcharge the batteries or even damage them.
I cannot find any such circuit on the net, all I have found refer to single batteries or pair, not 10 in series.
Some help is appreciated.
I have an adsl router at home (like most) and a small computer (mini server) connected to it.
The computer is an Alix-1D and consumes only 5W max at 12V.
I want to build a small UPS for these two, so that it can keep them up and running when power is lost. Mostly interested in sudden power loss, a few minutes max (which happens oftenly) and not long time power loss. Note, only 12v DC output is needed, not conversion to 220v AC.
I want to use 10 low self discharge AA NiMH batteries connected in series to produce about 12v, just what the computer and the router needs.
A simple UPS can be as simple as this one
with two diodes.
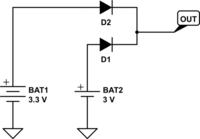
However this does not charge the batteries, so I need a circuit to charge these 10 NiMH batteries connected in series. I need this circuit to be safe, not exploding the batteries, as it is for home use. So something like this
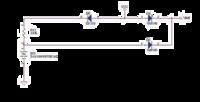
[found at www .electronics -circuits .com /schematics /embedded /battery -backup .png[/url]
is not good probably as will overcharge the batteries or even damage them.
I cannot find any such circuit on the net, all I have found refer to single batteries or pair, not 10 in series.
Some help is appreciated.
Last edited by a moderator: