manohar.sathish
Newbie level 4
HI, I am using SG3525A for controlling Push-Pull Converter.
Our entire circuit comprises of Dc-Dc section , followed by a DC-AC section. Its a 800VA Home Inverter.
DC-Dc Specifications:
Push pull configuration
Input Voltage : 10-17V DC
Input current : 80A @ 10V Input
Output : 350V DC nominal
Watts : 800VA
DC-AC Specification:
Full Bridge configuration,20KHz
Output Voltage : 230V AC nominal
Output current: 4.44A Max
The inverter section alone tested at full load (upto 600W) and its working fine.
DC-Dc Section tested at no load (with input range 10V-17V) @ 100Khz, 56Khz,16Khz
But I am facing issues in the integration of DC-DC and DC-AC section.
1) @ 56KHz For Input voltage upto 10V-15V the AC output is fine. But if Ie increase the voltage above 15V , the DC Link Voltage & AC output Flickers.( for 40W & 60W load tested)
SG3525A : Rt =4.7KOhm, Ct=2.7NF, Css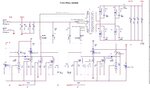
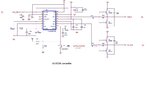
=1uF
2) @100KHz For input voltage upto 10V-15V the AC output is fine. But if Ie increase the voltage above 15V , the DC Link Voltage & AC output Flickers..( for 40W & 60W load tested)
SG3525A : Rt =4.7KOhm, Ct=1.5nF, Css=1uF
For both cases, Transformer used is :
Core : ETD 54 Ferrite
Turns ratio: 2:65
Frequency range : upto 500KHz.
Kindly suggest a solution for this flickering and instability issue.
Our entire circuit comprises of Dc-Dc section , followed by a DC-AC section. Its a 800VA Home Inverter.
DC-Dc Specifications:
Push pull configuration
Input Voltage : 10-17V DC
Input current : 80A @ 10V Input
Output : 350V DC nominal
Watts : 800VA
DC-AC Specification:
Full Bridge configuration,20KHz
Output Voltage : 230V AC nominal
Output current: 4.44A Max
The inverter section alone tested at full load (upto 600W) and its working fine.
DC-Dc Section tested at no load (with input range 10V-17V) @ 100Khz, 56Khz,16Khz
But I am facing issues in the integration of DC-DC and DC-AC section.
1) @ 56KHz For Input voltage upto 10V-15V the AC output is fine. But if Ie increase the voltage above 15V , the DC Link Voltage & AC output Flickers.( for 40W & 60W load tested)
SG3525A : Rt =4.7KOhm, Ct=2.7NF, Css
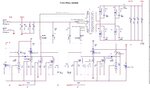
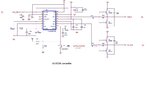
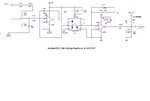
2) @100KHz For input voltage upto 10V-15V the AC output is fine. But if Ie increase the voltage above 15V , the DC Link Voltage & AC output Flickers..( for 40W & 60W load tested)
SG3525A : Rt =4.7KOhm, Ct=1.5nF, Css=1uF
For both cases, Transformer used is :
Core : ETD 54 Ferrite
Turns ratio: 2:65
Frequency range : upto 500KHz.
Kindly suggest a solution for this flickering and instability issue.