jatayu
Newbie level 5
- Joined
- May 17, 2010
- Messages
- 9
- Helped
- 0
- Reputation
- 0
- Reaction score
- 0
- Trophy points
- 1,281
- Location
- Jogjakarta
- Activity points
- 1,345
i have project, and one of the problem is i must drive a heater that use 220VAC/50Hz suply, use PWM signal 24VDC.
i need use the PWM duty cycle to cut the 220VAC phase.
but all circuit that i try to design cant work.
please anyone help me. i need circuit that the input is PWM24VDC and 220VAC/50Hz. and the output is 220VAC/50HZ which the phase is cutted. this is the time diagram of the signals that i want
the first signal is the 220VAC
the second signal is the PWM signal
and the third signal is the output that i want
best regards
jatayu
i need use the PWM duty cycle to cut the 220VAC phase.
but all circuit that i try to design cant work.
please anyone help me. i need circuit that the input is PWM24VDC and 220VAC/50Hz. and the output is 220VAC/50HZ which the phase is cutted. this is the time diagram of the signals that i want
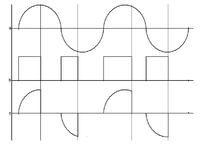
the first signal is the 220VAC
the second signal is the PWM signal
and the third signal is the output that i want
best regards
jatayu