KitWasHere
Newbie level 3
So I'm building an automotive electrical tester and I'm running into space constraints. The device is used to probe wires to see if they are at 12v or ground, apply 12v or ground to test components (power a headlight or fan directly), and to load test a circuit. The device is powered from the vehicle's battery.
Right now I'm using an automotive relay (really big) to act as short circuit protection. Press the button and it latches the relay, and the voltage at the zener is enough to hold it closed. Power shorted to ground will make the zener circuit hiccup and turn off the relay coil. The maximum load this tester could see is around 20-30 amps. (this is a simplified circuit, all the testing stuff would be after the relay. Full schematic at the bottom of the post):
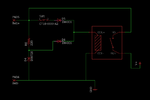
I'm wondering if anyone could point me in the right direction to replace this circuit with a mosfet or something of the like. Size is more important than cost for this, the relay takes up almost half of the enclosure!
Here is a full schematic in case that can help someone help me, or if someone wants to build they're own:
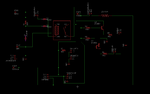
"Batt- Aux" is the negative lead for the voltmeter. The switch either connects this probe to battery ground, or leaves it floating so you can test the ground on the circuit.
This was not my idea, I just added a few features to it: https://www.instructables.com/id/Power-Logic-Probe/
Any help is really appreciated.
Right now I'm using an automotive relay (really big) to act as short circuit protection. Press the button and it latches the relay, and the voltage at the zener is enough to hold it closed. Power shorted to ground will make the zener circuit hiccup and turn off the relay coil. The maximum load this tester could see is around 20-30 amps. (this is a simplified circuit, all the testing stuff would be after the relay. Full schematic at the bottom of the post):
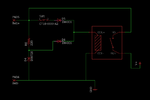
I'm wondering if anyone could point me in the right direction to replace this circuit with a mosfet or something of the like. Size is more important than cost for this, the relay takes up almost half of the enclosure!
Here is a full schematic in case that can help someone help me, or if someone wants to build they're own:
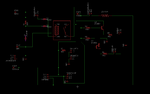
"Batt- Aux" is the negative lead for the voltmeter. The switch either connects this probe to battery ground, or leaves it floating so you can test the ground on the circuit.
This was not my idea, I just added a few features to it: https://www.instructables.com/id/Power-Logic-Probe/
Any help is really appreciated.
Last edited by a moderator: