Electro nS
Full Member level 6
Hello Guys
i have used this circuit (i found online last year) to drive big dc motors without much thinking but with great success
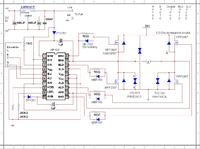
but yesterday i noticed something , there are 3 TVS (from each motor terminal to GND, and from VCC to GND) BUT THEY ARE BIDIRECTIONAL
now i am thinking , isn't it better to use Unidirectional instead in such circuit . another aspect , should i add 2 more tvs across the high side mosfets also ??
please give your opinion , maybe these diodes are not needed at all NOTE : i am using locked antiphase or sign magnitude drive methods WITH synchronous rectification
thanks and regards
i have used this circuit (i found online last year) to drive big dc motors without much thinking but with great success
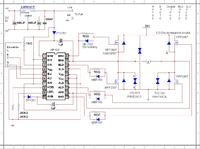
but yesterday i noticed something , there are 3 TVS (from each motor terminal to GND, and from VCC to GND) BUT THEY ARE BIDIRECTIONAL
now i am thinking , isn't it better to use Unidirectional instead in such circuit . another aspect , should i add 2 more tvs across the high side mosfets also ??
please give your opinion , maybe these diodes are not needed at all NOTE : i am using locked antiphase or sign magnitude drive methods WITH synchronous rectification
thanks and regards
Last edited: